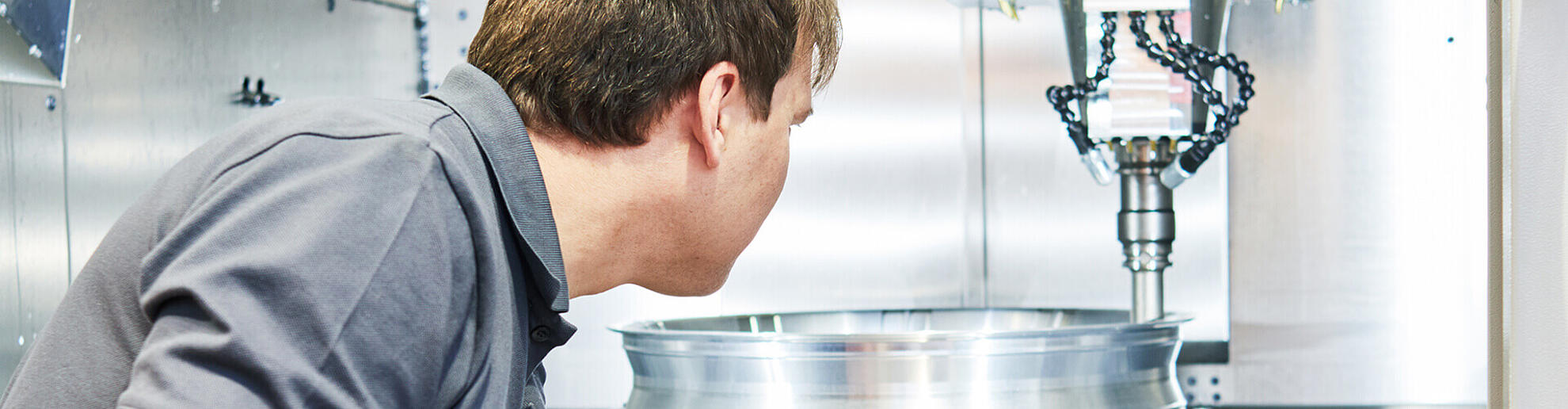
Tool casting from Silbitz
At the three foundry locations of the Silbitz Group in Silbitz, Košice and Zeitz there are 11 different furnaces available for the production of different cast parts in the full-mould casting process made of cast steel and cast iron for the tool technology sector in the automobile industry. Our foundries have a molding facility, a mechanical and manual hand molding shop. Furthermore, at our location in Stassfurt, it is also possible to mechanically process these parts.
Materials used
With a weight range of the individual parts from 5 kilograms to 45 tons, tool technology is primarily produced for the rail automotive industry. The materials that are used such as spheroidal graphite iron, grey cast iron and cast steel are in demand worldwide and are used for cutting attachments, upper and lower parts, stamps, holding down clamps and cutting knives. The materials used include cast iron with spheroidal graphite according to DIN EN 1563, cast iron with lamellar graphite according to DIN EN 1561, austenitic cast iron according to DIN EN 13835 (upon request), high-strength cast steel with good weldability according to SEW 520, cast steel GS and special steel casting GX for general applications according to DIN EN 10293, cryogenic cast steel according to SEW 685, tempering cryogenic steel according to SEW 510 or special steels according to customer needs. Within our group of companies, there are a large number of annealing furnaces available for the heat treatment departments. This is where the required micro-structural changes of the material can be produced through air hardening, isothermal annealing, ferritisation, soft annealing or stress-relief annealing. After hardening the annealing material can be rapidly cooled down by means of quench hardening in the cooling chamber and ventilators with maximum loading of up to 60 tons.
Safety in the quality of tool technology
As a result of our many years of experience in the production of such parts in tool technology, it is possible for us to guarantee the safety in the quality and design of the cast parts that are in demand. Close cooperation between constructors, modellers and casters is essential for the optimisation of the process chain in tool technology. Specialist advice on questions pertaining to tool technology, modelling and foundry technology is a prerequisite for achieving the goals set in the full-mould casting process. This includes short delivery times, optimal quality and high process reliability that are supported by the necessary CAQ systems, casting simulation programmes and data transmission possibilities.