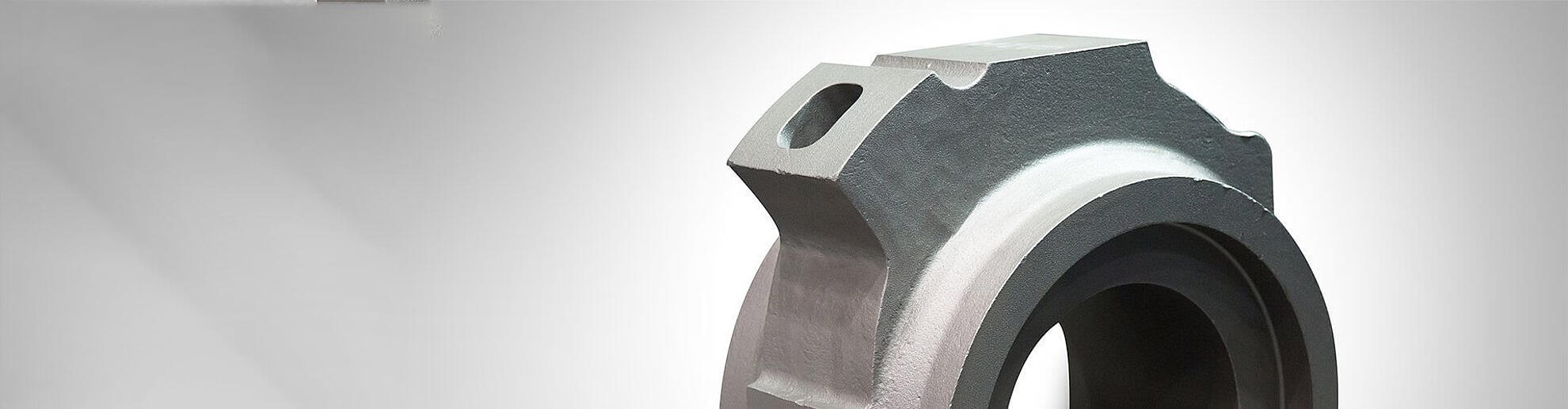
Full mold casting - cost-effective production of even complicated components
Full mold casting is a modern casting process for the production of components. Even complex functional parts with cavities can be produced cost-effectively. Full mold castings made of cast iron or cast steel are possible. After casting, the intact and therefore functional condition is checked in strict internal test procedures. Only after successful testing are the components delivered to customers, such as the automotive industry, mechanical engineering and other sectors.
Description of the full mold casting
Full mold casting is created by the process of full mold casting. In this process, red-hot molten metal made of iron or steel is poured into a solid mold. In contrast to other casting processes, there is no need to add a binding agent to the sand around the solid model. This protects the environment and saves costs for preparing the cast parts.
Features of objects made from solid castings
Depending on the molten metal used, objects made from solid castings are made from iron or cast steel. However, they are all characterized by a seamlessly intact shape with only minimal post-processing. Complicated components with or without cavities can be produced with a particularly precise fit using full mold casting. The durability of solid castings makes them resistant to wear. This is important, for example, for the high loads on components in the automotive industry or in machines and systems. The PS-E models can be manufactured in automated production. This means that large quantities can be produced in a short time at low cost.
Production of components from full mold casting
Before components are produced from full mold casting, a workpiece is manufactured from PS-E (polystyrene) in a one-to-one size ratio. Depending on the planned shape, this can also involve several parts, which are assembled before casting. A coating (protective layer) is applied over the ready-to-cast model. It is then placed in a container filled with molding sand. During casting, the PS-E styrofoam model is gasified. The resulting gas is extracted through the molding sand. During the casting process, there is no direct contact between the sand and the melt. The sand can therefore be reused for new molds afterwards. At the end of full mold casting, the workpiece remains in the mold until it solidifies. It is then removed and adapted to the further specifications according to the order description.
Silbitz is your contact for full mold casting
Full mold casting significantly simplifies the production of even complex components for vehicles, machines and systems. Preparation can be automated cost-effectively for medium quantities. The process is also one of the most environmentally friendly manufacturing processes. For example, the molding sand remains free of binders and can therefore be reused several times. We would be happy to advise you on this. Get in touch with us now!