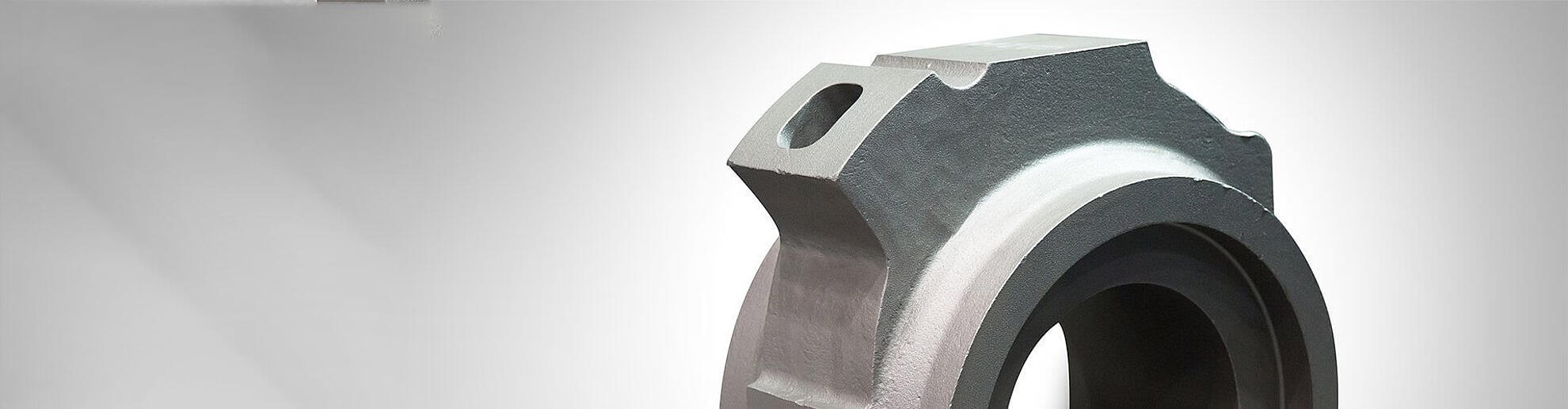
Foundry
Foundries can look back on a long history, as the melting of iron and subsequent casting into prefabricated molds has been known since ancient times.
The foundry Silbitz Group offers the highest level of innovation
As a foundry company for cast iron and cast steel, the Silbitz Group is following this trend not only in terms of innovation in the IT sector, but also in terms of the innovative implementation of the results provided by the research department and the in-house development department. This refers in particular to the improvement of material properties, which combines the optimization of the casting process with the customer-specific performance required. This also includes border areas, such as the redevelopment or reconstruction of forging made of isothermal tempered cast iron with ductile iron, ADI. Through the targeted interaction of computer-aided processes in the organization, production and logistics as well as a casting technology on the highest level of technology, the Silbitz Group can respond to specific customer requirements by direct forming quickly and offer solutions. This extends to ready-to-install components and also includes post-processing by means of machining technology.
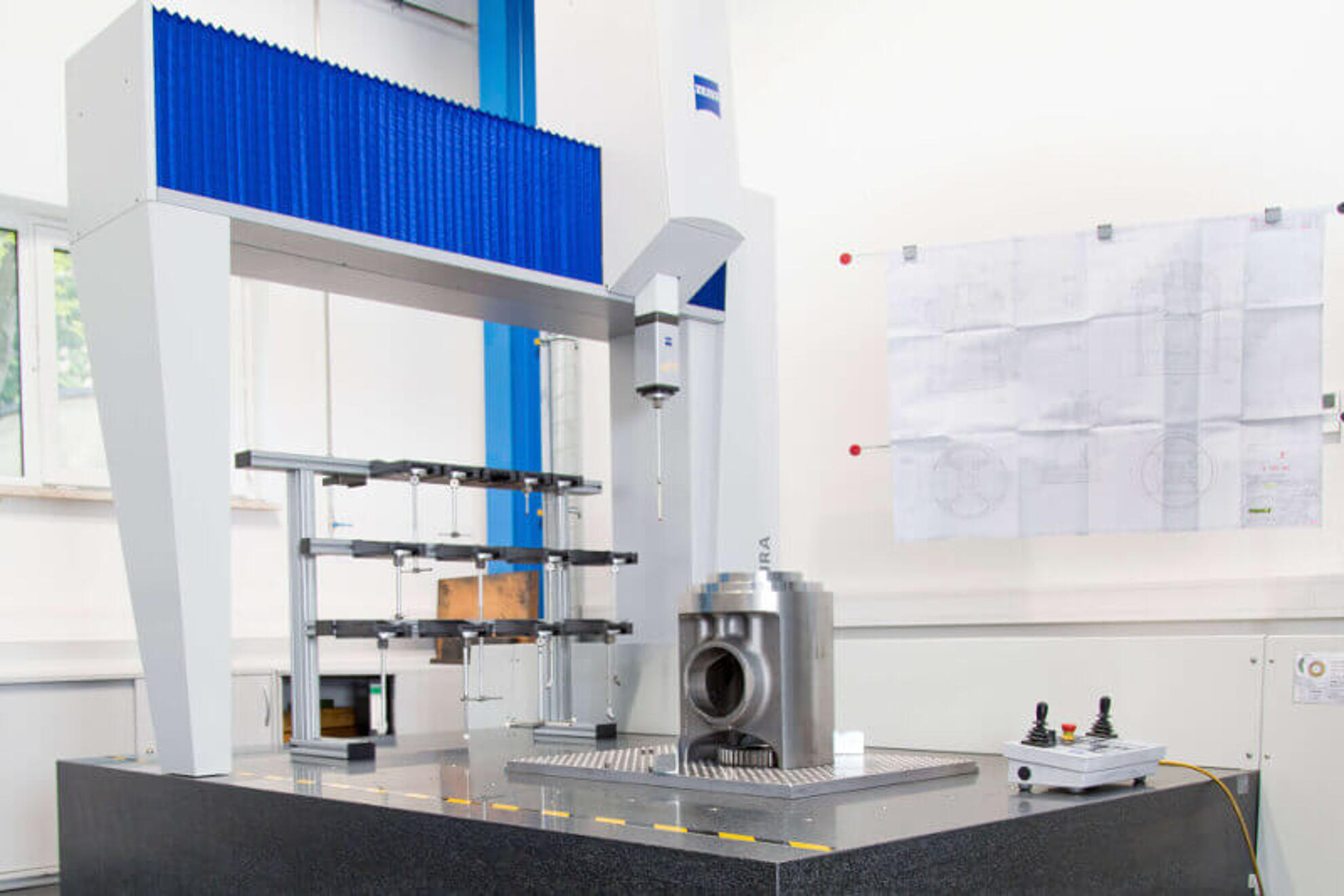
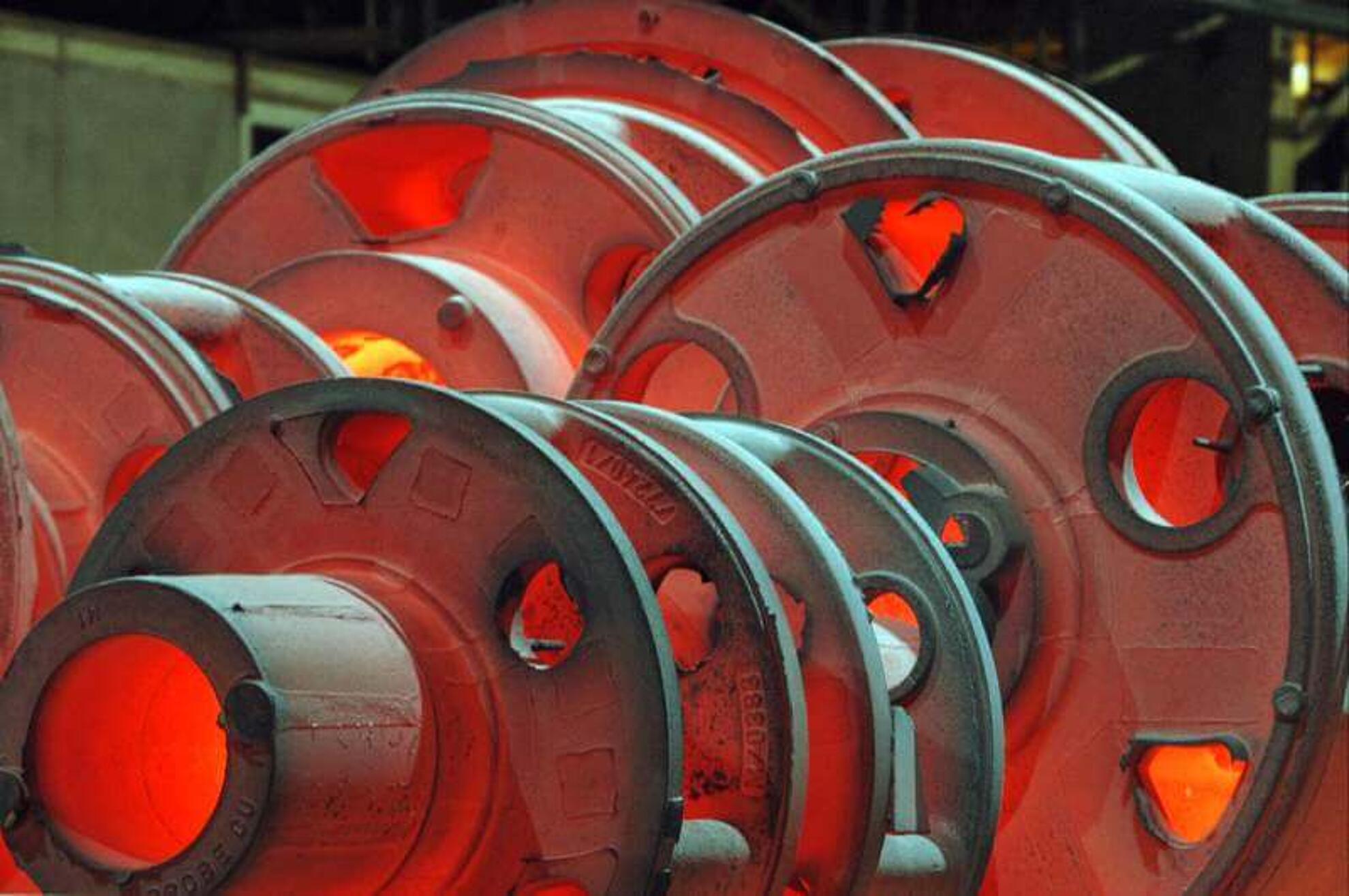
The technology of the steel and iron foundry
The melting of iron and the subsequent casting in prefabricated forms has been known since ancient times. Although, it was not possible to speak of a technology in the present sense at this time, the results were astonishing.
The challenge for historic foundries was on the one hand the high melting point of iron and on the other hand the correct mixing ratio of iron and carbon, from where the different names for iron and steel originate. Every iron with a carbon content of 2% is called steel today. About 2 % is usually traded under cast iron, while pure iron barely appears. The secret in earlier times was to divert or admit carbon. Since the melting furnaces in the former foundries mostly consisted of natural stone and the melting point had to be achieved with hard coal, large amounts of melt were not yet possible and impurities could not be prevented either. Only modern blast furnaces, which operated with coke and which were provided with refractory linings, allowed for greater smelting and more rational processes. By blowing in oxygen, it was then possible to eliminate further impurities, which resulted in increasingly high-quality steels and cast iron.
Modern casting technology in the age of chips and EDP
Great development over centuries and sensational research results in metallurgy, especially in the nineteenth and twentieth centuries, produced unimagined achievements in foundry technology. In the second half of the twentieth century, the introduction of the arc furnace seemed to have achieved an optimum in terms of melting and casting processes and in the development of automatic processes. In the meantime, however, EDP has created yet another innovative revolution that has led to revolutionaly developments in terms of production processes, the control of casting processes and the planning and construction of cast parts. However, the possibilities are far from exhausted and new advances in IT are finding their way into the practical application of modern foundry technology. This also intervenes in mold making, where CAD design programs and CNC machine tools have revolutionized mold production in recent decades. Another step is direct forming. This method makes it possible to produce molds for prototypes and individual pieces withour models.
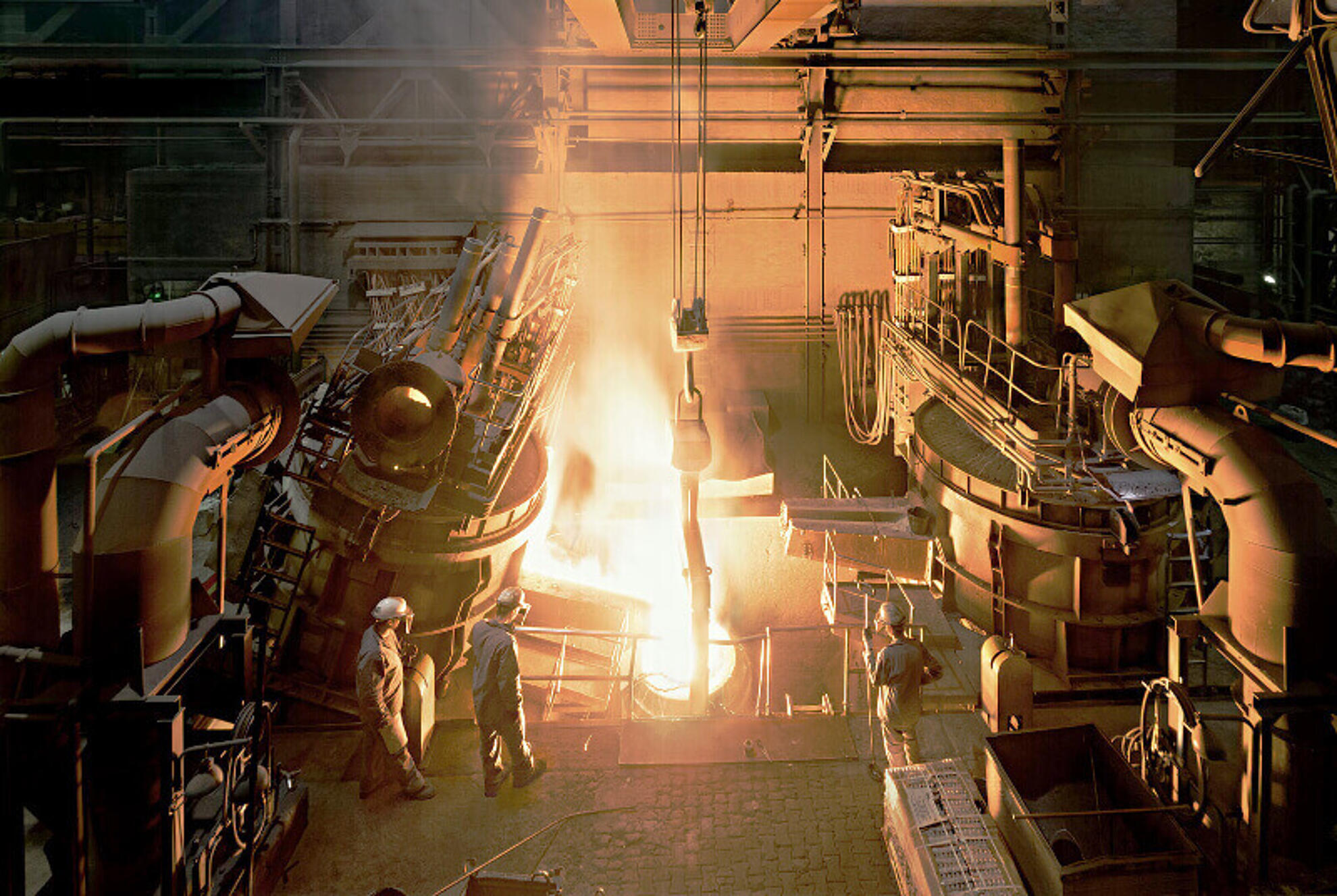
Our locations
Silbitz Guss GmbH
Dr.-Maruschky-Straße 2
07613 Silbitz
Germany
Telephone: +49 36693 129694
Fax: +49 36693 80 255
E-Mail: info[at]silbitz-group.com
ZGG - Zeitzer Guss GmbH
Naumburger Straße 52
06712 Zeitz
Deutschland
Telephone: +49 3441 22871 10
Fax: +49 3441 2287 120
E-Mail: info[at]silbitz-group.com
EUROCAST Košice, s.r.o.
Vstupný areal U.S. Steel
04454 Košice – Šaca
Germany
Telephone: +421 918 555 700
Fax: +421 55 673 7087
E-Mail: info[at]silbitz-group.com
E-Mail: etickalinka[at]silbitz-group.com
Silbitz Group Stassfurt AWS GmbH
An der Liethe 5
39418 Stassfurt
Germany
Telephone: +49 3925 960 402
Fax: +49 3925 960 405
E-Mail: sgs-info[at]silbitz-group.com